Press release
Iron Ore Production Process with Cost Analysis: Comprehensive Insights into Market Drivers, Raw Material Needs, and Production Costs
Iron ore is a crucial raw material in steel production and various industrial applications, making it a cornerstone of modern manufacturing. This report provides a detailed overview of the Iron Ore Production Process with Cost Analysis, covering procurement resource assessment, market drivers, raw material requirements, and production costs. For mining companies, steel manufacturers, and investors, this guide offers essential insights into the iron ore production process and factors influencing its cost structure.
Request Free Sample - https://shorturl.at/aQO5o
Procurement Resource Assessment: Iron Ore Production Process
Iron ore production begins with a thorough procurement resource assessment to ensure efficient, sustainable operations. Key resources required for production include mining equipment, energy, labor, and access to high-grade iron ore reserves. Effective procurement of these resources supports cost-efficient production and consistent output quality.
Key components of procurement resource assessment include:
High-Grade Iron Ore Reserves: The quality of iron ore reserves directly impacts production efficiency and final product quality. Companies often secure mining rights to high-grade ore deposits through governmental permits or partnerships with resource owners, ensuring long-term access to essential raw materials.
Iron Ore Production Process - https://shorturl.at/9LYrg
Mining Equipment and Infrastructure: Iron ore production requires heavy machinery, including excavators, loaders, haul trucks, and crushing and screening equipment. Additionally, robust infrastructure, such as access roads, power supply, and transportation systems, is essential to support mining operations. Investing in energy-efficient and durable equipment is critical for cost-effective production.
Skilled Labor and Technological Expertise: Skilled personnel are needed to manage operations, including mining engineers, geologists, equipment operators, and processing technicians. Employing trained staff ensures that mining activities are conducted safely, efficiently, and in compliance with environmental regulations.
Energy Resources: Iron ore extraction and processing are energy-intensive, requiring electricity, diesel fuel, and water. Access to reliable energy sources, such as grid electricity or on-site generators, is essential to support the continuous operation of mining and processing equipment.
A comprehensive procurement resource assessment helps iron ore producers secure the necessary inputs for efficient operations, maintain high-quality output, and optimize production costs.
Understanding Iron Ore and Its Applications
Iron ore is a mineral-rich rock that contains iron oxides, which can be extracted and refined to produce metallic iron. The primary use of iron ore is in steelmaking, where it serves as a fundamental raw material. Steel, in turn, is essential for construction, infrastructure, transportation, manufacturing, and a wide array of consumer goods.
Applications of iron ore include:
Steel Production: Iron ore is the primary raw material in steelmaking. The ore is processed in a blast furnace or direct reduction process, where it is combined with carbon sources, such as coke, to produce molten iron. This molten iron is then refined to create steel, which is used in construction, automotive manufacturing, and various other industries.
Iron-Based Products: Beyond steel, iron ore is used in the production of iron-based products, such as cast iron, which is widely used in machinery, automotive parts, and cookware.
Industrial Applications: Iron ore is also utilized in industrial applications, including the production of catalysts for chemical processes, water treatment, and pigments for paints and coatings.
Due to its essential role in steel production, iron ore is a highly sought-after commodity, supporting the global construction and manufacturing sectors.
Market Drivers Influencing Iron Ore Production
The production and demand for iron ore are influenced by several market drivers, including industrial growth, infrastructure development, and technological advancements. Understanding these drivers is essential for mining companies, steel producers, and investors to make informed decisions about their operations and strategies.
Global Demand for Steel: The construction, automotive, and manufacturing industries drive demand for steel, which directly impacts the demand for iron ore. As countries invest in infrastructure development and urbanization, the need for steel-and thus iron ore-continues to grow. Emerging economies, particularly in Asia, are significant drivers of this demand.
Technological Advancements in Steelmaking: Technological advancements in steelmaking, such as electric arc furnaces (EAFs) and direct reduction processes, are reshaping the demand for specific types of iron ore. Producers must adapt to these technological changes by investing in processing capabilities that align with market needs.
Environmental and Sustainability Trends: The push for sustainability and reducing carbon emissions is influencing the iron ore market. Some steelmakers are shifting towards more sustainable practices, such as using low-carbon steel production methods. This trend is expected to increase demand for high-grade iron ore that reduces emissions in the steelmaking process.
Global Economic Conditions: Iron ore prices are influenced by global economic conditions, as economic growth typically drives demand for steel-intensive projects. During periods of economic expansion, demand for iron ore increases, while economic slowdowns can lead to reduced demand and lower prices.
Government Policies and Trade Agreements: Government policies and trade agreements between major iron ore producers and consumers significantly impact the market. For example, export tariffs, import restrictions, and trade tensions between countries like China and Australia can influence global iron ore prices and availability.
By understanding these market drivers, iron ore producers can align their strategies to meet industry demand, capitalize on sustainability trends, and navigate the complexities of the global marketplace.
Raw Materials Requirements for Iron Ore Production
The production of iron ore primarily requires access to high-quality ore deposits, along with additional resources for extraction and processing. Key raw material requirements include:
Iron Ore Deposits: Securing access to high-grade iron ore deposits is essential for efficient production. The quality of the ore, including its iron content and the presence of impurities, determines the ease of processing and the final product quality. Producers often engage in exploration and geological surveys to identify and assess potential mining sites.
Fuel and Energy Sources: Diesel fuel is required to power heavy mining equipment, while electricity is used for processing and beneficiation stages. Water is also essential for ore processing, cooling machinery, and controlling dust during extraction.
Blasting and Drilling Materials: In open-pit mining, blasting materials, such as ammonium nitrate fuel oil (ANFO), are used to break up the ore for easier extraction. Drilling equipment and other specialized tools are also required for accessing deeper ore deposits.
Processing Reagents: During beneficiation, processing reagents are used to separate iron ore from impurities. These may include flocculants, collectors, and depressants, depending on the specific beneficiation process.
By managing these raw material requirements effectively, producers can optimize the extraction and processing stages, control costs, and ensure the quality of iron ore for downstream steelmaking applications.
Costs and Key Process Information
The cost of producing iron ore depends on various factors, including mining expenses, labor costs, equipment investment, and energy usage. Additionally, production costs vary based on the scale of production, facility location, and technological advancements in mining and processing.
Mining and Extraction Costs: The cost of mining iron ore includes expenses for drilling, blasting, hauling, and loading. Mining costs are affected by the depth and quality of the ore body, as well as the efficiency of the equipment used. Open-pit mining is commonly used for iron ore extraction, and economies of scale can help reduce unit costs for larger operations.
Energy Costs: Iron ore production is energy-intensive, particularly during beneficiation and refining stages. Energy expenses for electricity and fuel significantly impact total production costs. Many facilities invest in energy-efficient equipment and renewable energy sources to reduce operational costs and minimize environmental impact.
Labor and Compliance Costs: Skilled personnel, including equipment operators, engineers, and quality control specialists, are essential for safe and efficient mining operations. Labor costs vary depending on the location and production scale, while compliance with environmental regulations and safety standards contributes to operational expenses.
Equipment and Maintenance: The initial investment in mining and processing equipment, such as crushers, separators, and conveyors, is substantial. Ongoing maintenance is necessary to ensure operational efficiency and prevent production downtime. Producers must also budget for periodic equipment upgrades or replacements to remain competitive.
Regulatory Compliance and Environmental Management: Iron ore production must adhere to environmental regulations, including emissions control, waste management, and land rehabilitation. Compliance costs, such as emissions control systems and water treatment facilities, are necessary for sustainable operations and regulatory approval.
Looking for an Exhaustive and Personalized Report?
For businesses seeking a comprehensive understanding of the iron ore production process with cost analysis, a personalized and exhaustive report can provide valuable insights. Such a report includes detailed cost breakdowns, profitability forecasts, and customized recommendations for optimizing production, enhancing efficiency, and expanding market reach. Whether you aim to scale your operations, explore new market opportunities, or improve process efficiency, an industry-specific report can substantiate your business strategies with data-driven analysis.
With thorough market data, cost projections, and strategic guidance, a customized report on iron ore production empowers you to make informed decisions that drive growth, sustainability, and profitability in your business.
Contact Us:
Company Name: Procurement Resource
Contact Person: Amanda Williams
Email: sales@procurementresource.com
Toll-Free Number: USA Canada - Phone no: +1 307 363 1045 | UK - Phone no: +44 7537 132103 | Asia-Pacific (APAC) - Phone no: +91 1203185500
Address: 30 North Gould Street, Sheridan, WY 82801, USA
About Us:
Procurement Resource is an invaluable partner for businesses seeking comprehensive market research and strategic insights across a spectrum of industries. With a repository of over 500 chemicals, commodities, and utilities, updated regularly, they offer a cost-effective solution for diverse procurement needs. Their team of seasoned analysts conducts thorough research, delivering clients with up-to-date market reports, cost models, price analysis, and category insights.
By tracking prices and production costs across various goods and commodities, Procurement Resource ensures clients receive the latest and most reliable data. Collaborating with procurement teams across industries, they provide real-time facts and pioneering practices to streamline procurement processes and enable informed decision-making. Procurement Resource empowers clients to navigate complex supply chains, understand industry trends, and develop strategies for sustainable growth.
Request Free Sample - https://shorturl.at/aQO5o
Procurement Resource Assessment: Iron Ore Production Process
Iron ore production begins with a thorough procurement resource assessment to ensure efficient, sustainable operations. Key resources required for production include mining equipment, energy, labor, and access to high-grade iron ore reserves. Effective procurement of these resources supports cost-efficient production and consistent output quality.
Key components of procurement resource assessment include:
High-Grade Iron Ore Reserves: The quality of iron ore reserves directly impacts production efficiency and final product quality. Companies often secure mining rights to high-grade ore deposits through governmental permits or partnerships with resource owners, ensuring long-term access to essential raw materials.
Iron Ore Production Process - https://shorturl.at/9LYrg
Mining Equipment and Infrastructure: Iron ore production requires heavy machinery, including excavators, loaders, haul trucks, and crushing and screening equipment. Additionally, robust infrastructure, such as access roads, power supply, and transportation systems, is essential to support mining operations. Investing in energy-efficient and durable equipment is critical for cost-effective production.
Skilled Labor and Technological Expertise: Skilled personnel are needed to manage operations, including mining engineers, geologists, equipment operators, and processing technicians. Employing trained staff ensures that mining activities are conducted safely, efficiently, and in compliance with environmental regulations.
Energy Resources: Iron ore extraction and processing are energy-intensive, requiring electricity, diesel fuel, and water. Access to reliable energy sources, such as grid electricity or on-site generators, is essential to support the continuous operation of mining and processing equipment.
A comprehensive procurement resource assessment helps iron ore producers secure the necessary inputs for efficient operations, maintain high-quality output, and optimize production costs.
Understanding Iron Ore and Its Applications
Iron ore is a mineral-rich rock that contains iron oxides, which can be extracted and refined to produce metallic iron. The primary use of iron ore is in steelmaking, where it serves as a fundamental raw material. Steel, in turn, is essential for construction, infrastructure, transportation, manufacturing, and a wide array of consumer goods.
Applications of iron ore include:
Steel Production: Iron ore is the primary raw material in steelmaking. The ore is processed in a blast furnace or direct reduction process, where it is combined with carbon sources, such as coke, to produce molten iron. This molten iron is then refined to create steel, which is used in construction, automotive manufacturing, and various other industries.
Iron-Based Products: Beyond steel, iron ore is used in the production of iron-based products, such as cast iron, which is widely used in machinery, automotive parts, and cookware.
Industrial Applications: Iron ore is also utilized in industrial applications, including the production of catalysts for chemical processes, water treatment, and pigments for paints and coatings.
Due to its essential role in steel production, iron ore is a highly sought-after commodity, supporting the global construction and manufacturing sectors.
Market Drivers Influencing Iron Ore Production
The production and demand for iron ore are influenced by several market drivers, including industrial growth, infrastructure development, and technological advancements. Understanding these drivers is essential for mining companies, steel producers, and investors to make informed decisions about their operations and strategies.
Global Demand for Steel: The construction, automotive, and manufacturing industries drive demand for steel, which directly impacts the demand for iron ore. As countries invest in infrastructure development and urbanization, the need for steel-and thus iron ore-continues to grow. Emerging economies, particularly in Asia, are significant drivers of this demand.
Technological Advancements in Steelmaking: Technological advancements in steelmaking, such as electric arc furnaces (EAFs) and direct reduction processes, are reshaping the demand for specific types of iron ore. Producers must adapt to these technological changes by investing in processing capabilities that align with market needs.
Environmental and Sustainability Trends: The push for sustainability and reducing carbon emissions is influencing the iron ore market. Some steelmakers are shifting towards more sustainable practices, such as using low-carbon steel production methods. This trend is expected to increase demand for high-grade iron ore that reduces emissions in the steelmaking process.
Global Economic Conditions: Iron ore prices are influenced by global economic conditions, as economic growth typically drives demand for steel-intensive projects. During periods of economic expansion, demand for iron ore increases, while economic slowdowns can lead to reduced demand and lower prices.
Government Policies and Trade Agreements: Government policies and trade agreements between major iron ore producers and consumers significantly impact the market. For example, export tariffs, import restrictions, and trade tensions between countries like China and Australia can influence global iron ore prices and availability.
By understanding these market drivers, iron ore producers can align their strategies to meet industry demand, capitalize on sustainability trends, and navigate the complexities of the global marketplace.
Raw Materials Requirements for Iron Ore Production
The production of iron ore primarily requires access to high-quality ore deposits, along with additional resources for extraction and processing. Key raw material requirements include:
Iron Ore Deposits: Securing access to high-grade iron ore deposits is essential for efficient production. The quality of the ore, including its iron content and the presence of impurities, determines the ease of processing and the final product quality. Producers often engage in exploration and geological surveys to identify and assess potential mining sites.
Fuel and Energy Sources: Diesel fuel is required to power heavy mining equipment, while electricity is used for processing and beneficiation stages. Water is also essential for ore processing, cooling machinery, and controlling dust during extraction.
Blasting and Drilling Materials: In open-pit mining, blasting materials, such as ammonium nitrate fuel oil (ANFO), are used to break up the ore for easier extraction. Drilling equipment and other specialized tools are also required for accessing deeper ore deposits.
Processing Reagents: During beneficiation, processing reagents are used to separate iron ore from impurities. These may include flocculants, collectors, and depressants, depending on the specific beneficiation process.
By managing these raw material requirements effectively, producers can optimize the extraction and processing stages, control costs, and ensure the quality of iron ore for downstream steelmaking applications.
Costs and Key Process Information
The cost of producing iron ore depends on various factors, including mining expenses, labor costs, equipment investment, and energy usage. Additionally, production costs vary based on the scale of production, facility location, and technological advancements in mining and processing.
Mining and Extraction Costs: The cost of mining iron ore includes expenses for drilling, blasting, hauling, and loading. Mining costs are affected by the depth and quality of the ore body, as well as the efficiency of the equipment used. Open-pit mining is commonly used for iron ore extraction, and economies of scale can help reduce unit costs for larger operations.
Energy Costs: Iron ore production is energy-intensive, particularly during beneficiation and refining stages. Energy expenses for electricity and fuel significantly impact total production costs. Many facilities invest in energy-efficient equipment and renewable energy sources to reduce operational costs and minimize environmental impact.
Labor and Compliance Costs: Skilled personnel, including equipment operators, engineers, and quality control specialists, are essential for safe and efficient mining operations. Labor costs vary depending on the location and production scale, while compliance with environmental regulations and safety standards contributes to operational expenses.
Equipment and Maintenance: The initial investment in mining and processing equipment, such as crushers, separators, and conveyors, is substantial. Ongoing maintenance is necessary to ensure operational efficiency and prevent production downtime. Producers must also budget for periodic equipment upgrades or replacements to remain competitive.
Regulatory Compliance and Environmental Management: Iron ore production must adhere to environmental regulations, including emissions control, waste management, and land rehabilitation. Compliance costs, such as emissions control systems and water treatment facilities, are necessary for sustainable operations and regulatory approval.
Looking for an Exhaustive and Personalized Report?
For businesses seeking a comprehensive understanding of the iron ore production process with cost analysis, a personalized and exhaustive report can provide valuable insights. Such a report includes detailed cost breakdowns, profitability forecasts, and customized recommendations for optimizing production, enhancing efficiency, and expanding market reach. Whether you aim to scale your operations, explore new market opportunities, or improve process efficiency, an industry-specific report can substantiate your business strategies with data-driven analysis.
With thorough market data, cost projections, and strategic guidance, a customized report on iron ore production empowers you to make informed decisions that drive growth, sustainability, and profitability in your business.
Contact Us:
Company Name: Procurement Resource
Contact Person: Amanda Williams
Email: sales@procurementresource.com
Toll-Free Number: USA Canada - Phone no: +1 307 363 1045 | UK - Phone no: +44 7537 132103 | Asia-Pacific (APAC) - Phone no: +91 1203185500
Address: 30 North Gould Street, Sheridan, WY 82801, USA
About Us:
Procurement Resource is an invaluable partner for businesses seeking comprehensive market research and strategic insights across a spectrum of industries. With a repository of over 500 chemicals, commodities, and utilities, updated regularly, they offer a cost-effective solution for diverse procurement needs. Their team of seasoned analysts conducts thorough research, delivering clients with up-to-date market reports, cost models, price analysis, and category insights.
By tracking prices and production costs across various goods and commodities, Procurement Resource ensures clients receive the latest and most reliable data. Collaborating with procurement teams across industries, they provide real-time facts and pioneering practices to streamline procurement processes and enable informed decision-making. Procurement Resource empowers clients to navigate complex supply chains, understand industry trends, and develop strategies for sustainable growth.
Permanent link to this press release:
Copy
Please set a link in the press area of your homepage
to this press release on woodPRI. woodPRI disclaims liability for any content contained in
this release.
Recommend
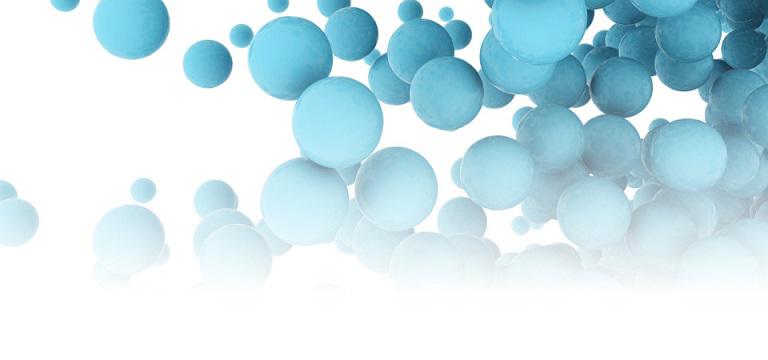
/newsMicroencapsulation Market Deep Analysis on Key Players - Dow Corning, Encapsys, Syngenta Crop Protection, Evonik Industries, 3M and Bayer
Market Study Report Adds Global Microencapsulation Market Size, Status and Forecast 2024 added to its database. The report provides key statistics on the current state of the industry and other analytical data to understand the market.
Extensive research is required for choosing the appropriate cor...
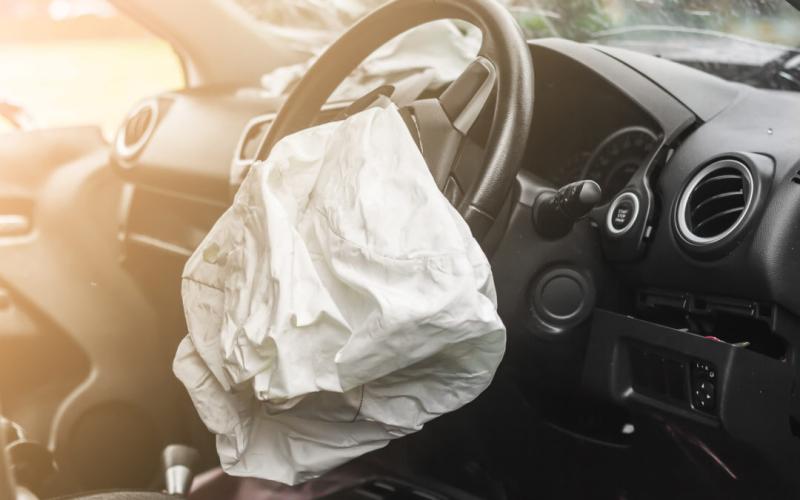
/newsGermany Airbag Market Size 2023: Global Share, Industry And Report Analysis By 2030 | Hyundai Mobis Co., Ltd. Key Safety Systems, Inc. Robert Bosch GmbH
Germany airbag market is expected to grow at a CAGR of around 6% during the forecast period. Germany Airbag Market research report refers to gathering and analyzing significant market data serve as best medium for various industry players to launch novel product or service. It is vital for key firms...
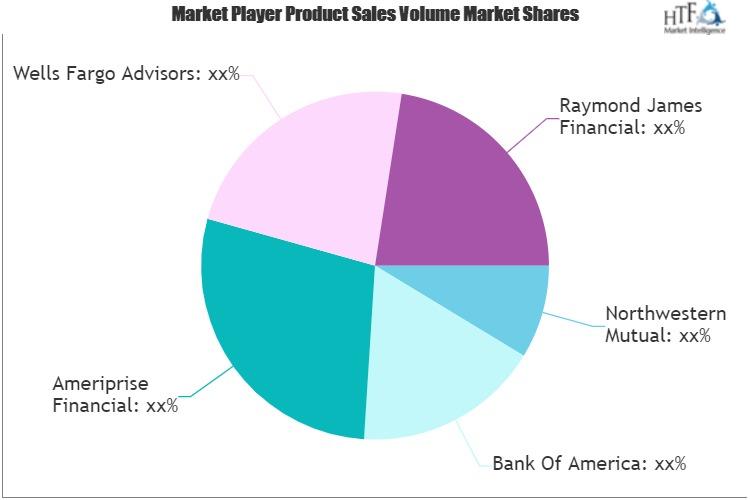
/newsSecurities Brokerages And Stock Exchanges Market Outlook 2021: Big Things are Happening
A new intelligence report released by HTF MI with title "Global Securities Brokerages And Stock Exchanges Market Survey & Outlook" is designed covering micro level of analysis by Insurers and key business segments, offerings and sales channels. The Global Securities Brokerages And Stock Exchange...
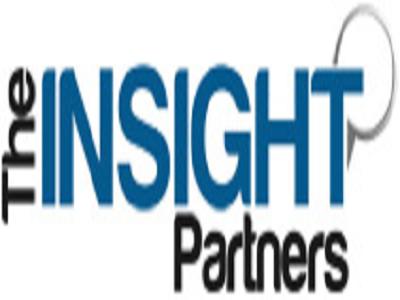
/newsRenewable Chemicals Market Emerging Trends and Competitive Landscape Forecast to 2028
The renewable chemicals market was valued at US$ 80,566.30 million in 2021 and is projected to reach US$ 1,76,750.76 million by 2028 it is expected to grow at a CAGR of 11.9% from 2021 to 2028. The research report focuses on the current market trends, opportunities, future potential of the market, a...
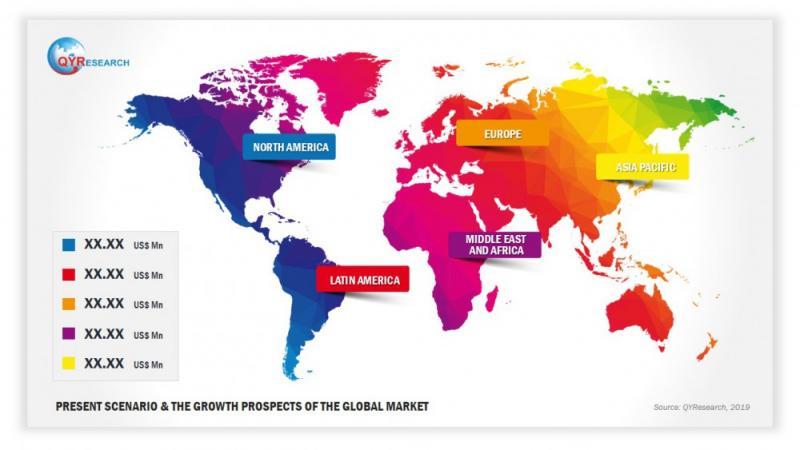
/newsHow Coronavirus is Impacting Cold Brew Coffee, Global Market Volume Analysis, Size, Share and Key Trends 2020-2026
"Market Latest Research Report 2020:
Los Angles United States, February 2020: The Cold Brew Coffee market has been garnering remarkable momentum in the recent years. The steadily escalating demand due to improving purchasing power is projected to bode well for the global market. QY Research's lates...
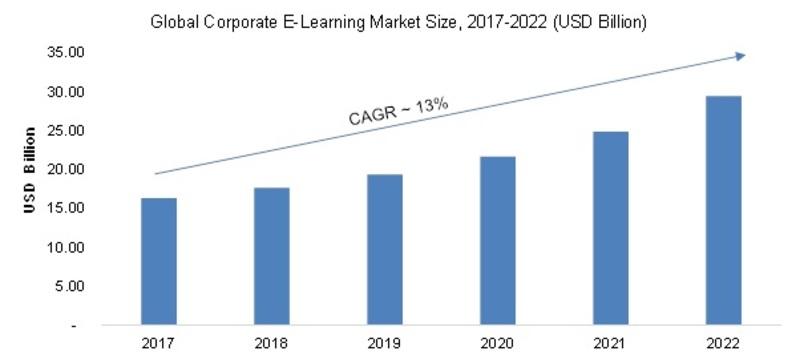
/newsCorporate E-Learning Market - Global Industry Size, Share, Key Players Analysis that are Infor, SkillSoft Corporation, Adrenna, CERTPOINT Systems and others with Regional Forecast to 2022
Overview:
E-Learning is used to enhance the learning procedures for newer job requirements and to make employees sound about the internal and external changes in the market and respective organizations. This method has created considerable differences in the ways of training and developing employee...