Press release
Understanding the Natural Gas Production Cost
Natural gas is one of the most widely used energy sources globally, playing a critical role in electricity generation, heating, and as a raw material in industrial applications. Its relatively clean-burning nature makes it a preferred alternative to coal and oil for reducing greenhouse gas emissions. However, the cost of producing natural gas is influenced by numerous factors, from exploration and drilling to processing and transportation.
Natural Gas Production Cost: https://shorturl.at/medut
This article provides a detailed examination of the factors that influence natural gas production costs, covering topics such as exploration, extraction, labor, equipment, environmental compliance, and strategies for reducing expenses while maintaining operational efficiency.
Exploration and Drilling Costs
Exploring potential natural gas reserves and drilling are significant cost components in natural gas production. These costs are incurred during the initial phases of production and are essential for identifying viable reserves.
Request For Free Sample: https://shorturl.at/vagGr
Seismic Surveys and Geological Studies: Before drilling, companies conduct extensive seismic surveys and geological studies to identify potential natural gas reserves. These surveys involve using sound waves to create images of subsurface formations, helping to assess the feasibility of extraction. The costs of seismic surveys depend on the technology used, the size of the exploration area, and the complexity of the terrain.
Drilling and Well Development: Once a site is deemed viable, the next step is drilling. Drilling costs vary based on the depth of the well, type of drilling technology used, and geographic location. For offshore sites, drilling costs are generally higher due to the added complexity of underwater operations. Horizontal and hydraulic fracturing techniques, commonly used for shale gas, also increase drilling expenses due to the advanced equipment and additional materials required.
Permitting and Regulatory Compliance: Exploration and drilling require various permits and licenses, which contribute to upfront costs. The regulatory environment can significantly impact these costs, as stricter regulations may necessitate additional studies, inspections, and reporting. Delays in obtaining permits or compliance requirements can also increase expenses.
The exploration and drilling stages represent a high-risk investment, as companies may not always discover commercially viable quantities of natural gas. Successful exploration is essential for cost-effective production, as it determines the potential profitability of the project.
Extraction Costs
Once natural gas reserves have been located, the next stage is extraction. Extraction costs are affected by the type of gas field, extraction method, and production technology used.
Types of Gas Fields:
Conventional Gas Fields: These are generally easier and cheaper to extract because the gas is often trapped in large reservoirs and flows freely to the surface.
Unconventional Gas Fields: Shale gas, tight gas, and coal bed methane are examples of unconventional gas sources. Extracting natural gas from these sources is more complex and requires advanced techniques like hydraulic fracturing, which significantly raises costs.
Hydraulic Fracturing and Horizontal Drilling: In unconventional gas fields, companies often use hydraulic fracturing (fracking) and horizontal drilling to access the gas trapped in tight rock formations. These methods involve injecting high-pressure water, sand, and chemicals into the well to fracture the rock and release the gas. Fracking and horizontal drilling are resource-intensive and require specialized equipment, which adds to extraction costs.
Water and Chemical Use: The fracking process requires large volumes of water and various chemicals. Procuring, transporting, and disposing of these materials adds to the cost, particularly in regions with limited water availability or strict disposal regulations. Some companies are exploring the use of recycled water to lower costs and reduce environmental impact.
Well Maintenance and Stimulation: Over time, natural gas wells may require maintenance and stimulation to maintain productivity. Techniques such as acidizing, which involves injecting acid into the well to dissolve blockages, and re-fracturing can extend the life of a well but also increase operating costs.
Extraction costs are influenced by factors such as the complexity of the reservoir, the depth of the well, and the techniques employed. Technological advancements in drilling and extraction can improve efficiency and reduce these costs over time.
Processing Costs
Natural gas extracted from wells typically contains impurities, including water, sulfur compounds, and hydrocarbons like ethane, propane, and butane. Processing is necessary to remove these impurities and produce marketable natural gas.
Separation: The first step in processing involves separating natural gas from oil, water, and other components. Separation equipment, such as scrubbers and separators, is used to remove these substances. The cost of separation depends on the composition of the raw gas and the types of contaminants present.
Dehydration: Natural gas is dehydrated to remove water vapor, which can condense and form hydrates that block pipelines. Common dehydration methods include glycol dehydration and desiccant dehydration. These methods require equipment and energy, adding to processing costs.
Sweetening: Natural gas often contains hydrogen sulfide (H₂S) and carbon dioxide (CO₂), which must be removed to meet pipeline and environmental standards. This process, known as gas sweetening, involves using amine solvents or other chemicals to absorb these impurities. Sweetening is particularly costly in areas with high sulfur content, as it requires additional equipment and chemicals.
NGL Recovery: In some cases, natural gas liquids (NGLs), such as ethane, propane, and butane, are extracted and sold separately. The recovery of NGLs requires additional processing equipment, such as cryogenic distillation units. NGL recovery is beneficial for revenue generation, but it adds complexity and cost to the overall process.
Processing costs are influenced by the composition of the raw natural gas, the required purity level, and the equipment used. Improvements in processing technologies, such as more efficient separation and sweetening methods, can help reduce costs.
Transportation and Storage Costs
Transporting natural gas from production sites to end users requires an extensive infrastructure network, including pipelines, storage facilities, and, in some cases, liquefied natural gas (LNG) terminals.
Pipelines: Pipelines are the most common method of transporting natural gas. The cost of pipeline construction depends on the distance, terrain, and regulatory requirements. For offshore production, underwater pipelines are often necessary, which are more expensive to install and maintain than onshore pipelines. Pipeline transportation also involves ongoing maintenance, monitoring, and safety checks.
LNG Infrastructure: For international markets or areas without pipeline access, natural gas is often converted into LNG. The liquefaction process involves cooling the gas to extremely low temperatures, which requires specialized equipment and significant energy. LNG terminals are capital-intensive and costly to operate, making LNG a more expensive transportation option.
Storage Facilities: Natural gas storage is essential to manage supply and demand fluctuations, particularly for seasonal demand in the energy market. Storage facilities, such as underground reservoirs or LNG storage tanks, incur construction, maintenance, and monitoring costs. Storage is especially important for markets where gas demand varies significantly throughout the year.
Transportation and storage costs are heavily influenced by factors such as distance to markets, availability of infrastructure, and transportation method. Companies often invest in partnerships with pipeline operators or LNG facilities to optimize transportation and reduce costs.
Regulatory Compliance Costs
The natural gas industry is highly regulated to ensure safety, environmental protection, and resource management. Regulatory compliance is an ongoing expense, as companies must adhere to local, national, and international regulations.
Environmental Permits: Natural gas production requires permits related to land use, air emissions, water usage, and waste disposal. Obtaining these permits involves upfront costs, as well as ongoing expenses for monitoring and reporting. Strict environmental regulations, such as those on methane emissions, can increase compliance costs.
Health and Safety Standards: Companies must comply with health and safety regulations to protect workers and nearby communities. This involves regular inspections, safety training, and investments in equipment like blowout preventers and fire suppression systems. Compliance with health and safety standards is critical to prevent accidents and avoid fines.
Emissions Control: Methane is a potent greenhouse gas, and controlling methane emissions is a priority for regulatory bodies. Companies invest in leak detection and repair (LDAR) programs, as well as technologies to capture and reduce methane emissions. While these measures add to production costs, they are essential for regulatory compliance and for reducing environmental impact.
Ensuring regulatory compliance is essential for operational stability and maintaining a positive reputation. Companies often invest in staff training and conduct regular audits to verify adherence to industry standards and avoid fines.
Environmental and Waste Management Costs
Natural gas production has various environmental impacts, including emissions, water usage, and waste generation. Environmental management costs are associated with mitigating these impacts and complying with environmental regulations.
Water Management: Hydraulic fracturing requires significant water usage, and the water often becomes contaminated with chemicals and underground minerals. Treating and disposing of wastewater, or finding alternative uses for it, adds to production costs. Some companies invest in on-site water treatment facilities to recycle water and reduce costs.
Methane Capture and Reduction: Methane emissions occur during extraction, processing, and transportation. Companies use equipment like vapor recovery units and invest in technologies to capture methane and prevent it from entering the atmosphere. Methane reduction is costly but essential for reducing the environmental footprint of natural gas production.
Waste Disposal: Natural gas production generates various forms of waste, including drilling mud, fracking fluids, and contaminated soil. Proper disposal involves treating hazardous waste and transporting it to approved disposal sites, which is a significant expense for producers. Waste minimization and recycling initiatives can help reduce disposal costs.
Contact Us:
Company Name: Procurement Resource
Contact Person: Leo Frank
Email: sales@procurementresource.com
Toll-Free Number: USA & Canada - Phone no: +1 307 363 1045 | UK - Phone no: +44 7537 132103 | Asia-Pacific (APAC) - Phone no: +91 1203185500
Address: 30 North Gould Street, Sheridan, WY 82801, USA
Procurement Resource is a premier market research firm dedicated to delivering in-depth insights and analysis on the procurement and production costs of a wide range of commodities and products. Backed by a team of experienced industry professionals, Procurement Resource provides detailed reports that encompass every aspect of the supply chain-from sourcing raw materials to final product manufacturing. Their services are tailored to help businesses enhance their procurement strategies, minimize costs, and improve overall efficiency. With robust market intelligence and proprietary cost models, Procurement Resource empowers clients to make well-informed decisions, remain competitive, and foster sustainable growth in today's dynamic market environment.
Natural Gas Production Cost: https://shorturl.at/medut
This article provides a detailed examination of the factors that influence natural gas production costs, covering topics such as exploration, extraction, labor, equipment, environmental compliance, and strategies for reducing expenses while maintaining operational efficiency.
Exploration and Drilling Costs
Exploring potential natural gas reserves and drilling are significant cost components in natural gas production. These costs are incurred during the initial phases of production and are essential for identifying viable reserves.
Request For Free Sample: https://shorturl.at/vagGr
Seismic Surveys and Geological Studies: Before drilling, companies conduct extensive seismic surveys and geological studies to identify potential natural gas reserves. These surveys involve using sound waves to create images of subsurface formations, helping to assess the feasibility of extraction. The costs of seismic surveys depend on the technology used, the size of the exploration area, and the complexity of the terrain.
Drilling and Well Development: Once a site is deemed viable, the next step is drilling. Drilling costs vary based on the depth of the well, type of drilling technology used, and geographic location. For offshore sites, drilling costs are generally higher due to the added complexity of underwater operations. Horizontal and hydraulic fracturing techniques, commonly used for shale gas, also increase drilling expenses due to the advanced equipment and additional materials required.
Permitting and Regulatory Compliance: Exploration and drilling require various permits and licenses, which contribute to upfront costs. The regulatory environment can significantly impact these costs, as stricter regulations may necessitate additional studies, inspections, and reporting. Delays in obtaining permits or compliance requirements can also increase expenses.
The exploration and drilling stages represent a high-risk investment, as companies may not always discover commercially viable quantities of natural gas. Successful exploration is essential for cost-effective production, as it determines the potential profitability of the project.
Extraction Costs
Once natural gas reserves have been located, the next stage is extraction. Extraction costs are affected by the type of gas field, extraction method, and production technology used.
Types of Gas Fields:
Conventional Gas Fields: These are generally easier and cheaper to extract because the gas is often trapped in large reservoirs and flows freely to the surface.
Unconventional Gas Fields: Shale gas, tight gas, and coal bed methane are examples of unconventional gas sources. Extracting natural gas from these sources is more complex and requires advanced techniques like hydraulic fracturing, which significantly raises costs.
Hydraulic Fracturing and Horizontal Drilling: In unconventional gas fields, companies often use hydraulic fracturing (fracking) and horizontal drilling to access the gas trapped in tight rock formations. These methods involve injecting high-pressure water, sand, and chemicals into the well to fracture the rock and release the gas. Fracking and horizontal drilling are resource-intensive and require specialized equipment, which adds to extraction costs.
Water and Chemical Use: The fracking process requires large volumes of water and various chemicals. Procuring, transporting, and disposing of these materials adds to the cost, particularly in regions with limited water availability or strict disposal regulations. Some companies are exploring the use of recycled water to lower costs and reduce environmental impact.
Well Maintenance and Stimulation: Over time, natural gas wells may require maintenance and stimulation to maintain productivity. Techniques such as acidizing, which involves injecting acid into the well to dissolve blockages, and re-fracturing can extend the life of a well but also increase operating costs.
Extraction costs are influenced by factors such as the complexity of the reservoir, the depth of the well, and the techniques employed. Technological advancements in drilling and extraction can improve efficiency and reduce these costs over time.
Processing Costs
Natural gas extracted from wells typically contains impurities, including water, sulfur compounds, and hydrocarbons like ethane, propane, and butane. Processing is necessary to remove these impurities and produce marketable natural gas.
Separation: The first step in processing involves separating natural gas from oil, water, and other components. Separation equipment, such as scrubbers and separators, is used to remove these substances. The cost of separation depends on the composition of the raw gas and the types of contaminants present.
Dehydration: Natural gas is dehydrated to remove water vapor, which can condense and form hydrates that block pipelines. Common dehydration methods include glycol dehydration and desiccant dehydration. These methods require equipment and energy, adding to processing costs.
Sweetening: Natural gas often contains hydrogen sulfide (H₂S) and carbon dioxide (CO₂), which must be removed to meet pipeline and environmental standards. This process, known as gas sweetening, involves using amine solvents or other chemicals to absorb these impurities. Sweetening is particularly costly in areas with high sulfur content, as it requires additional equipment and chemicals.
NGL Recovery: In some cases, natural gas liquids (NGLs), such as ethane, propane, and butane, are extracted and sold separately. The recovery of NGLs requires additional processing equipment, such as cryogenic distillation units. NGL recovery is beneficial for revenue generation, but it adds complexity and cost to the overall process.
Processing costs are influenced by the composition of the raw natural gas, the required purity level, and the equipment used. Improvements in processing technologies, such as more efficient separation and sweetening methods, can help reduce costs.
Transportation and Storage Costs
Transporting natural gas from production sites to end users requires an extensive infrastructure network, including pipelines, storage facilities, and, in some cases, liquefied natural gas (LNG) terminals.
Pipelines: Pipelines are the most common method of transporting natural gas. The cost of pipeline construction depends on the distance, terrain, and regulatory requirements. For offshore production, underwater pipelines are often necessary, which are more expensive to install and maintain than onshore pipelines. Pipeline transportation also involves ongoing maintenance, monitoring, and safety checks.
LNG Infrastructure: For international markets or areas without pipeline access, natural gas is often converted into LNG. The liquefaction process involves cooling the gas to extremely low temperatures, which requires specialized equipment and significant energy. LNG terminals are capital-intensive and costly to operate, making LNG a more expensive transportation option.
Storage Facilities: Natural gas storage is essential to manage supply and demand fluctuations, particularly for seasonal demand in the energy market. Storage facilities, such as underground reservoirs or LNG storage tanks, incur construction, maintenance, and monitoring costs. Storage is especially important for markets where gas demand varies significantly throughout the year.
Transportation and storage costs are heavily influenced by factors such as distance to markets, availability of infrastructure, and transportation method. Companies often invest in partnerships with pipeline operators or LNG facilities to optimize transportation and reduce costs.
Regulatory Compliance Costs
The natural gas industry is highly regulated to ensure safety, environmental protection, and resource management. Regulatory compliance is an ongoing expense, as companies must adhere to local, national, and international regulations.
Environmental Permits: Natural gas production requires permits related to land use, air emissions, water usage, and waste disposal. Obtaining these permits involves upfront costs, as well as ongoing expenses for monitoring and reporting. Strict environmental regulations, such as those on methane emissions, can increase compliance costs.
Health and Safety Standards: Companies must comply with health and safety regulations to protect workers and nearby communities. This involves regular inspections, safety training, and investments in equipment like blowout preventers and fire suppression systems. Compliance with health and safety standards is critical to prevent accidents and avoid fines.
Emissions Control: Methane is a potent greenhouse gas, and controlling methane emissions is a priority for regulatory bodies. Companies invest in leak detection and repair (LDAR) programs, as well as technologies to capture and reduce methane emissions. While these measures add to production costs, they are essential for regulatory compliance and for reducing environmental impact.
Ensuring regulatory compliance is essential for operational stability and maintaining a positive reputation. Companies often invest in staff training and conduct regular audits to verify adherence to industry standards and avoid fines.
Environmental and Waste Management Costs
Natural gas production has various environmental impacts, including emissions, water usage, and waste generation. Environmental management costs are associated with mitigating these impacts and complying with environmental regulations.
Water Management: Hydraulic fracturing requires significant water usage, and the water often becomes contaminated with chemicals and underground minerals. Treating and disposing of wastewater, or finding alternative uses for it, adds to production costs. Some companies invest in on-site water treatment facilities to recycle water and reduce costs.
Methane Capture and Reduction: Methane emissions occur during extraction, processing, and transportation. Companies use equipment like vapor recovery units and invest in technologies to capture methane and prevent it from entering the atmosphere. Methane reduction is costly but essential for reducing the environmental footprint of natural gas production.
Waste Disposal: Natural gas production generates various forms of waste, including drilling mud, fracking fluids, and contaminated soil. Proper disposal involves treating hazardous waste and transporting it to approved disposal sites, which is a significant expense for producers. Waste minimization and recycling initiatives can help reduce disposal costs.
Contact Us:
Company Name: Procurement Resource
Contact Person: Leo Frank
Email: sales@procurementresource.com
Toll-Free Number: USA & Canada - Phone no: +1 307 363 1045 | UK - Phone no: +44 7537 132103 | Asia-Pacific (APAC) - Phone no: +91 1203185500
Address: 30 North Gould Street, Sheridan, WY 82801, USA
Procurement Resource is a premier market research firm dedicated to delivering in-depth insights and analysis on the procurement and production costs of a wide range of commodities and products. Backed by a team of experienced industry professionals, Procurement Resource provides detailed reports that encompass every aspect of the supply chain-from sourcing raw materials to final product manufacturing. Their services are tailored to help businesses enhance their procurement strategies, minimize costs, and improve overall efficiency. With robust market intelligence and proprietary cost models, Procurement Resource empowers clients to make well-informed decisions, remain competitive, and foster sustainable growth in today's dynamic market environment.
Permanent link to this press release:
Copy
Please set a link in the press area of your homepage
to this press release on woodPRI. woodPRI disclaims liability for any content contained in
this release.
Recommend
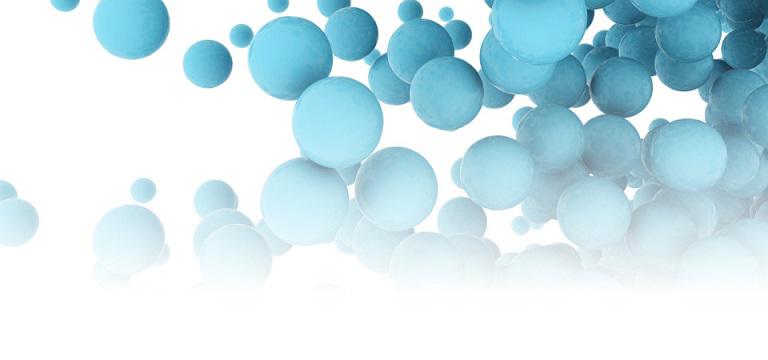
/newsMicroencapsulation Market Deep Analysis on Key Players - Dow Corning, Encapsys, Syngenta Crop Protection, Evonik Industries, 3M and Bayer
Market Study Report Adds Global Microencapsulation Market Size, Status and Forecast 2024 added to its database. The report provides key statistics on the current state of the industry and other analytical data to understand the market.
Extensive research is required for choosing the appropriate cor...
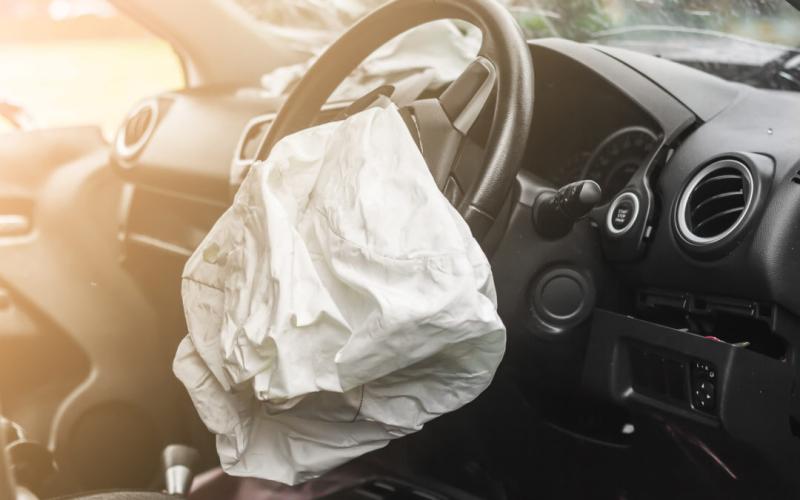
/newsGermany Airbag Market Size 2023: Global Share, Industry And Report Analysis By 2030 | Hyundai Mobis Co., Ltd. Key Safety Systems, Inc. Robert Bosch GmbH
Germany airbag market is expected to grow at a CAGR of around 6% during the forecast period. Germany Airbag Market research report refers to gathering and analyzing significant market data serve as best medium for various industry players to launch novel product or service. It is vital for key firms...
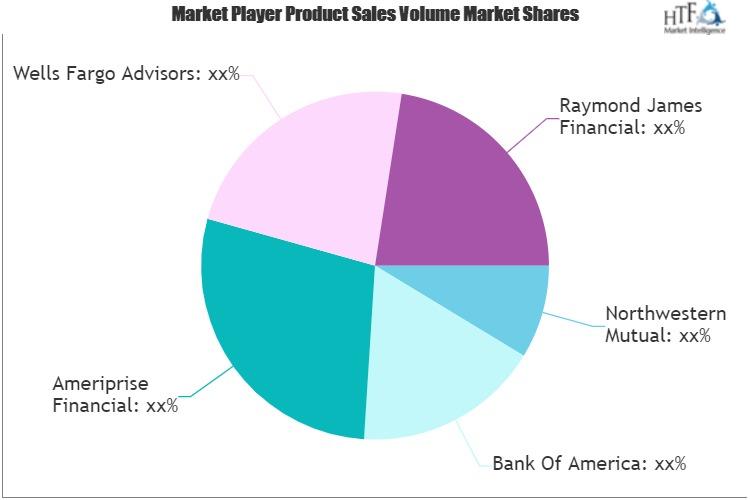
/newsSecurities Brokerages And Stock Exchanges Market Outlook 2021: Big Things are Happening
A new intelligence report released by HTF MI with title "Global Securities Brokerages And Stock Exchanges Market Survey & Outlook" is designed covering micro level of analysis by Insurers and key business segments, offerings and sales channels. The Global Securities Brokerages And Stock Exchange...
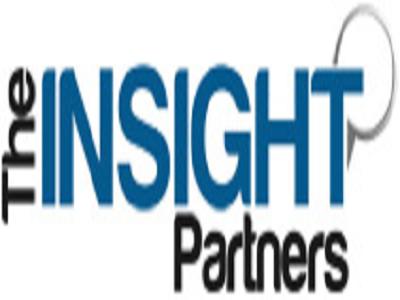
/newsRenewable Chemicals Market Emerging Trends and Competitive Landscape Forecast to 2028
The renewable chemicals market was valued at US$ 80,566.30 million in 2021 and is projected to reach US$ 1,76,750.76 million by 2028 it is expected to grow at a CAGR of 11.9% from 2021 to 2028. The research report focuses on the current market trends, opportunities, future potential of the market, a...
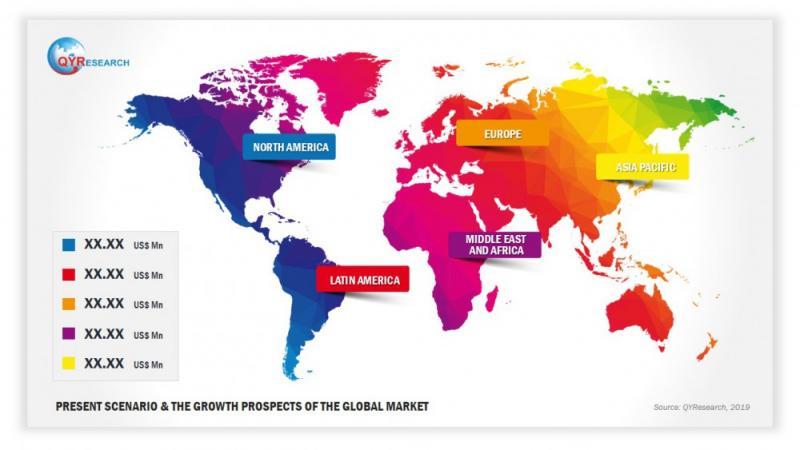
/newsHow Coronavirus is Impacting Cold Brew Coffee, Global Market Volume Analysis, Size, Share and Key Trends 2020-2026
"Market Latest Research Report 2020:
Los Angles United States, February 2020: The Cold Brew Coffee market has been garnering remarkable momentum in the recent years. The steadily escalating demand due to improving purchasing power is projected to bode well for the global market. QY Research's lates...
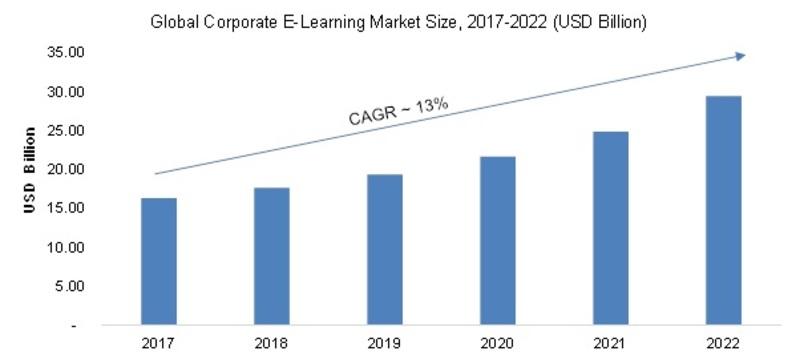
/newsCorporate E-Learning Market - Global Industry Size, Share, Key Players Analysis that are Infor, SkillSoft Corporation, Adrenna, CERTPOINT Systems and others with Regional Forecast to 2022
Overview:
E-Learning is used to enhance the learning procedures for newer job requirements and to make employees sound about the internal and external changes in the market and respective organizations. This method has created considerable differences in the ways of training and developing employee...